Here at Inoculate the World, we pride ourselves on “not being your average spore store.” It’s even in our slogan! But what does that really mean?
To us, it means making the highest quality product that we can. Which sometimes looks like going out of our way and even making extra work for ourselves to provide our customers with the purest spore syringes and most unique and interesting genetics we can find. Because that’s what we would expect when we order spores, and we would never serve our customers anything less.
So in the spirit of transparency, we thought we’d outline exactly what makes our process so special by explaining how our products are made.
Step One: We’re super selective
When you buy spores from Inoculate the World, you can be confident that you’re getting the “real deal” and not just any random mushroom spore. That’s because everything we provide has been intentionally selected to be the best possible quality.
For a lot of our strains, that begins when we’re out foraging. When we find mushrooms growing in the wild, we don’t just pick the first one we see and run to the lab to start busting out spore syringes. Instead, we take our time scoring fields and forests for the absolute best looking mushroom we can find. Usually, that means the biggest mushroom we encounter in a patch—from its cap to its stem—we look for the absolute strongest sample in the area that produces the most spores.
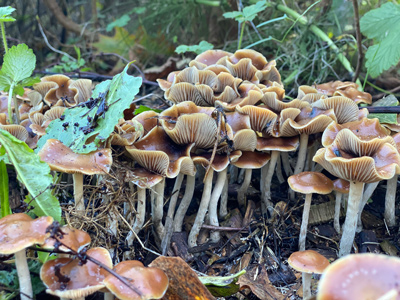
The same goes for how we choose spores from mushrooms cultivated by our friends in legal places, like Jamaica or the Netherlands. When they want to send us spores for the shop, we request they specifically collect them from the strongest mushrooms in their flush. So again, that means selecting the mushrooms that most resemble their strain, have the largest caps, and other characteristics people find interesting, like unique coloring.
The truth is, it’d be easier to just print everything that comes up, and probably more lucrative too, but then our genetics wouldn’t have the excellent reputation that they do. Because for us, it’s way more important to provide spores from the strongest mushrooms that best represent what that strain is all about, so our customers can study them in their optimal condition.
Step Two: We know exactly where everything is sourced
We don’t put any spores on the website that we don’t know their history. That means knowing where it was collected originally and by who. If it’s a domesticated strain, it also means knowing who cultivated and stabilized it. If it’s a hybrid strain, we also require knowing which strains were bred together to create it.
For landrace strains we collect ourselves, like our newest exclusive strain Tosohatchee cubensis, it’s easy because we can tell you exactly which field in the small town of Christmas, Florida we originally foraged it. But for more established strains in the mushroom community, like Albino Penis Envy (APE), it means tracing the strain’s history down to who originally sourced the spore print, and then who was cultivating the mushrooms to get to the stabilized generation that we all recognize.
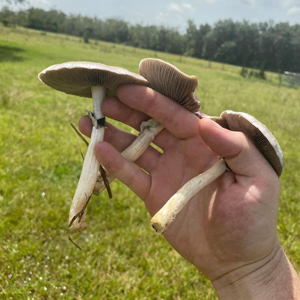
So, unless we know exactly where a strain came from and who brought them about, it stays in our hobby files. In fact, we have tons of really cool spores we’ve been gifted from customers and friends that we don’t feel comfortable putting on the site because we don’t know their full strain history.
But, that also means all of our customers can feel confident that they’re receiving legitimate spores when they order from us with no surprises.
Step Three: We DNA sequence our strains
Then, even though we’re confident about all our strains’ histories, we are working towards sequencing the DNA of our entire library to ensure that all of our spores are 100% from the mushrooms we say they are. We do this in partnership with Medicinal Genomics, a genetics science company that tests medicinal plants.
Our goal is that before we put a single spore on our site, we send it to Medicinal Genomics for their genome sequencing service, which has standards for different strains of Psilocybe cubensis as well as other species of magic mushrooms. Therefore, we’re working toward cross verifying every single one of our products on a genetic level, so there’s never any doubt over misrepresentation of the strains that we sell.
If you’re curious about learning more about the genetics of different strains of cubensis, check out Medicinal Genomics’s phylotree, Psilocydia. It’s a fascinating resource where a lot of our unique strains are represented!
Step Four: We take quality control seriously
Because we produce spore syringes and other spore products at scale, our biggest challenge is preventing contamination and maintaining sterility for all of our products. But even though we work at a large scale, we test everything for contaminants in small batches of 50 to 100 syringes.
The truth is, we could save hours of labor by testing in larger batches, but that would increase our risk of contamination, and we are not OK with that. For one, it would degrade our product, but it would also make our customers’ lives harder. So instead, our Lab Manager—who’s got a degree in molecular biology—and Assistant Production Manager came up with a process where we test every batch of spores before any syringes get put on the site.
When making spore syringes in the lab the first thing we do is crack out half gallon jars that are fitted with special lids, and mix the spores with sterilized distilled water. Then, the jars are put on a stir plate to blend it all up.
Jar of spore solution on a stir plate
Once the spore solution is mixed, we pull all of the syringes and let them sit for three to five days before testing them. What’s happening in that time is we’re allowing any hidden endospores or bacteria to really thrive and come alive. Some companies might test for contaminants right away—and most likely get clean results—but that wouldn’t be completely accurate because the potential bacteria in there hasn’t really had time to come alive and make itself known.
So instead, after our three to five day waiting period, we test our syringes by dripping spore solution on agar, and the we wait again. This is a crucial part of our quality control process, and takes an additional five to seven days before we have results, but it’s what makes us stand apart as having consistently containment-free products. If the results of our agar tests aren’t super clear, we repeat this step two to three times until we can get a clear reading, or we eliminate that batch all together.
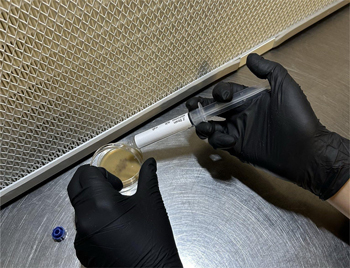
Dripping spore solution on agar
We do this in small batches of 50 to 100 syringes rather than larger ones of 1,000 or more to prevent contamination to our absolute best possible ability. Because when giant vats of liquid are used, there are more places for bacteria to sneak away and hide, only to come alive at the worst possible time—when it’s in our customer’s hands for scientific research.
Step Five: Everything gets a batch number
Then, once we’re certain our spores are clean and 100% free of contaminants, we give them a batch number and put the new syringes on the site.
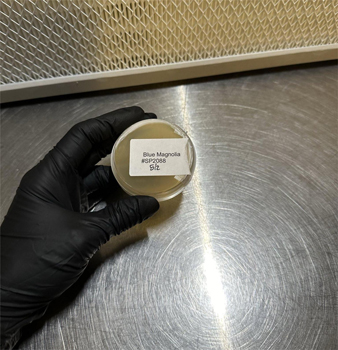
Batch numbers are also important because we track every single product we’ve ever created in our extensive database. That way, if a customer has an issue with a product, we can look back at the date it was created, what spore batch was used to make the product, who made it, and when it was tested for quality control, among other details.
What happens if something doesn’t pass quality control?
Batches that don’t make it through our strict quality control process are still documented in our database and we can still learn a ton from them, including what spores were used, what type of contamination was present, the date it was created, and who created it. This way we can backtrack and try to understand if the contamination was present in the spores or if something happened during our production process.
Contamination can happen for a number of reasons. Sometimes, it’s something as small as the seal on the jar wasn’t correct, other times, it’s the result of something not being sterilized properly or agar plates going bad. By being able to determine why something is contaminated we can then make decisions moving forward to create a better product.
Step Six: We provide full customer support
Even though we’re pretty confident in providing our customers with the cleanest possible products with the strongest possible genetics, we are still here to help! In fact, we’re the only spore store we know of with a full time customer support team.
So if you run into problems, have questions, or need help in any capacity, you can be certain that when you reach out to us for help, it’s a real life person on the other end of the line helping to solve your issue!
Conclusion
If you can’t already tell, we take great pride in our work here at Inoculate the World. We would never cut any corners when it comes to our products. Because just like you, we’re citizen scientists who are passionate about mushrooms and spores, and we’d only serve you all the best possible products that we would also expect. In fact, we’ve changed our technique and protocols many times over the years to ensure things are done the best possible way.
That way, you can place your orders with the peace of mind that you’re getting an intentionally made, high-quality and clean spore product created by people who care about rare and unique mushroom genetics, and want to share them with the world.